Yesterday, we had the opportunity to meet with an employee at PAM, the Physical Asset Management team. The seven employees at PAM have the difficult and important job of maintaining all machines and devices at Queen Elizabeth Central Hospital, as well as multiple other hospitals in Malawi; Catherine goes into more depth about the facts of PAM in her blog if you’re interested! Joseph, the PAM employee who we met with, graciously spent two hours of his afternoon giving us a tour around PAM, answering our numerous questions, describing the specific problems each device faced, and discussing the challenges that the department deals with.
PAM is housed in what looks like a warehouse, where broken medical devices line shelves and the floor. The machines range from suction pumps used in intensive care units, to incubators used in neonatal care wards, to surgical platforms, to CT scanners, to adult ventilators, to theatre lights—any medical device used in any of the seven hospitals PAM services is fair game to be sent to Blantyre, where these few employees must troubleshoot the malfunctioning device. This job description alone is daunting, however the technical expertise required is probably one of the lesser challenges PAM faces. Sometimes, the devices delivered to PAM cannot be fixed, but not because the employees don’t how to fix the machine—usually, they do. Instead, the obstacles standing in the way often fall into one of the following categories:
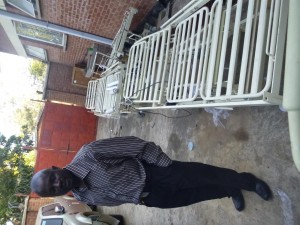
- Lack of Specific Parts. Many of the complex medical devices require very specific parts, often produced only by the original manufacturer, in order to function. When a device is broken due to a bum part—a blown electrical component, a worn out filter, a lost valve, a bent heating component—the first inclination is to replace that part with the same exact piece; this would ensure proper functionality. However, most of these components are absurdly expensive; we recently fixed a jaundice meter that wasn’t charging, and the original manufacturer was going to charge $1000 for replacement batteries, in addition to who knows how much more for troubleshooting the charging station. Due to this impracticality, alternative cheap components can sometimes be bought as replacements. While this works for some devices, for many others it will not. Sometimes, machines have control systems that disallow function if official components are not used; other times, the cheaper parts can damage the machine to a greater degree, or the cheap replacement components themselves break shortly after being implemented; in other cases, cheaper alternatives cannot be found due to the intricacy of a part. To add another layer of complexity, there is little consistency in the brand of device that various wards use. Many of the devices were either donations or not bought in bulk, so there can be multiple different brands of the same device even within QECH. In PAM, we probably saw upwards of 8 different types of oxygen concentrators. The part needed to repair this concentrator, then, also cannot be bought in bulk nor kept on hand. All of this results in many of the broken devices that arrive at PAM staying broken, as the materials are not available / the funding is not existent to make the repairs that the employees know need to happen.
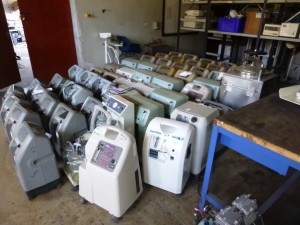
- Lack of Consumables. Increased use of consumables (device components that are frequently replaced, such as needles, syringes, etc.) often decrease the likelihood of a medical device being successful in low-resource settings. There’s a significant portion of devices at PAM that are most likely in working order, but the hospital doesn’t have the funding to supply the needed consumable to make the device useful. This is often an issue with donated devices. QECH receives many donated medical machines from various sources, but if the devices aren’t given with an adequate supply of consumables, the machines can’t be used as intended.
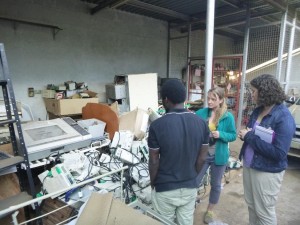
- Lack of Testing Equipment. Crucial to the process of fixing a broken device is the ability to test the device’s functionality. This was a problem that I hadn’t really considered before, but as we walked around PAM it became apparent how big an obstacle it created. For broken ventilators, a volume meter and a flow meter are needed to ensure the fixed device is truly delivering the amount of air it claims to be supplying; for broken phototherapy lights, a meter is needed to test the light intensity; sensitive temperature monitors are needed to fix incubators. However, it’s not feasible to buy and maintain testing equipment for each medical device that also needs to be bought and maintained. Without the proper testing equipment, many machines’ problems cannot be fully understood, while some fixed machines cannot be safely returned to the wards without first being tested.
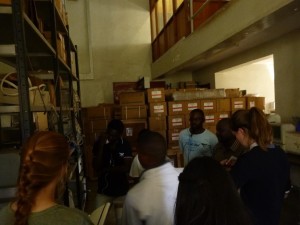
- Lack of Preventative Maintenance. Many of the medical devices require routine maintenance, from general cleaning, to replacing filters, to checking water levels and valves. Some of these practices can be completed by nurses in the wards, however this requires training. Other more complex preventative maintenance practices require a PAM engineer to visit the hospitals on an ideally quarterly basis. Since the majority of hospitals that PAM services are a long drive away, both training and in-person maintenance require fuel and lodging, which requires funding, which is already limited; in order to conduct this maintenance, funding must be allocated away from other crucial resources the hospital needs.
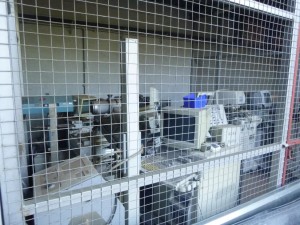
Touring PAM and learning about these obstacles was helpful in many ways. For one, it inspired design ideas that we will pursue in the remaining portion of our internship. We like the idea of taking an engineering based project needed by PAM and developing it with local materials, as the resulting device has a greater likelihood of being sustained over a brand new design project that we come up with on our own. We also can use PAM throughout the design process to gain feedback quickly, improving our chances of developing a successful device.
The trip to PAM was also an eye-opening peek into the varied and layered challenges that hospitals in low-resource settings face; the example challenges I’ve listed in this blog only scratch the surface of what the hospital must work through. As a student who hopes to enter the medical technology field in my future, there are hundreds of lessons to be learned about appropriate design through talking to and observing the processes at PAM. Design constraints extend into the complexity and rarity of the components chosen to construct the device, and consumable supply-chain problems can completely halt the use of a machine. If a device needs to be tested, the price and availability of the testing mechanism needs to be taken into account, as does the required maintenance. This first trip to PAM showed us how frustrating it can be to work with biomedical machines in this context, but it also inspired ideas about problems we can possibly solve as well as how to better design technologies in our future.