During matriculation, President Leebron began his address to our class by saying something along the lines of “We have people here from all around the world… Singapore, India, Germany… and Britton, Michigan – population 568.” As a nervous freshman starting school at a university over 1000 miles away from home, it was comforting to have my hometown mentioned in his welcome speech. It also reminded me, someone who has never traveled outside of North America, that there is a whole world out there filled with exceptional people, each with lives very different than my own. Over the course of my freshman year, I have met so many of these amazing people and been exposed to so many different ways of thinking. While working at the Polytechnic Design Studio this summer, not only am I excited to make an impact on the field of global health, but I am also excited to get to know my fellow interns from Malawi and Tanzania.
On June 3rd, Hannah, Nimisha, Shadé, Sally, and I will board a plane that will take us from Houston to London, to Johannesburg, to Lilongwe. From there, we will meet up with Liseth and Kyla, hop in a van, and ride for 4 hours to Blantyre. After many hours of travel, we will then finally rest at the Kabula Lodge and wake up the next morning ready for the start of our internship. But before all of this can happen, there is a lot of work that must be done…
360° Boot Camp
At the start of our two weeks of technology preparation in the OEDK, we found out that we will be taking 8 projects with us to Malawi…
- Mechanism to Lock IV Drip Rate
- Reusable Phototherapy Masks
- Automatic Bleach Sterilization Machine
- Neonatal Temperature Monitor for Kangaroo Mother Care
- Low-Cost Oxygen Monitoring System
- Ballard Score Gestational Age Training Model
- Cervical Cancer Screening Training Model
- Affordable Redesigned Ostomy Bags
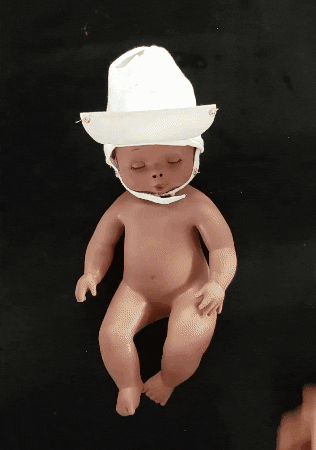
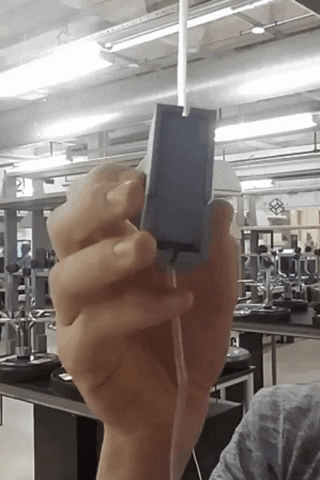
For the past week, I have been tag-teaming three of these projects with Shadé. Together we have sewn new phototherapy masks and 3D-printed more IV drip locks to present to the nurses at Queen Elizabeth Central Hospital. The masks are composed of a cotton hat and a flip down visor that prevents any blue light from damaging an infant’s retinas during phototherapy. The IV drip lock is a case that encloses the roller clamp used to adjust the dosage on an IV drip. The case can only be opened using a pen, allowing clinicians easy access to the roller clamp while keeping it away from patients or concerned family members who may want to adjust the dosage themselves.
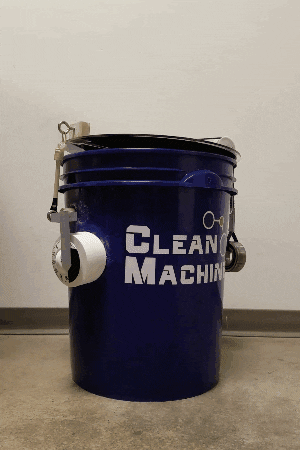
Our third technology that we took responsibility for is the automatic bleach sterilization machine (a.k.a. Clean Machine). Previous 360° interns found that doctors and nurses at Queen Elizabeth clean their tools in a solution of bleach and water; however, due to issues of under-staffing, the tools are often forgotten and left to soak for too long. As a result, the bleach eats away at the metal, and the tools have to be thrown out. Last semester, a team of students developed the Clean Machine, a device composed primarily of two ordinary buckets and a kitchen timer. The device allows nurses to load tools into the inner bucket, fill the outer bucket with the bleach solution, and set a timer for a specific soak time. To prepare this technology, we laser cut the acrylic components of the device and condensed some of the wooden components of the device into easily 3D-printed files. Once in Malawi, we plan on assembling the device, implementing it at Queen Elizabeth pending the feedback of the nurses, and leaving behind the CAD files at the Poly for future prototyping.
The Next Few Weeks…
With one more week of our boot camp to go, a lot of the Malawi team’s focus is going to shift towards planning for the setup of another design studio at the Malawi University of Science and Technology (MUST). Rice 360° has purchased supplies for the studio such as 3D printers, laser cutters, and other prototyping equipment. In addition to setting up these machines at the new studio, we hope to leave behind our knowledge of the engineering design process, culture of safety, and excitement for innovation that has rubbed off on each of us after spending countless hours at the OEDK.
Towards the end of next week, we’ll start to tackle the daunting task of packing everything we’re taking into as few suitcases as possible. Once that’s done, I’ll be on my way back to Michigan to spend two weeks at home before the rest of this adventure begins. Everyday our flight to Malawi grows closer, and I grow a little more nervous, but also a lot more excited about the whole experience.
June 3rd cannot come fast enough!
– Alex